Shale Shaker Screen Sizes
Shale shaker screen sizes is decided by shaker screens. Different shale shaker screens have different shale shaker screen sizes.
American Petroleum Institute has laid down the guidelines for solid control systems in drilling industry. However, the main purpose of this standardization was to provide the end user with a fair idea of what they are investing their money into, when the purchase a certain type of shaker screen.
Now, before we delve into the benchmarking by API, let us give you an overview of what the shaker screen is or why is it that important to be researched about?
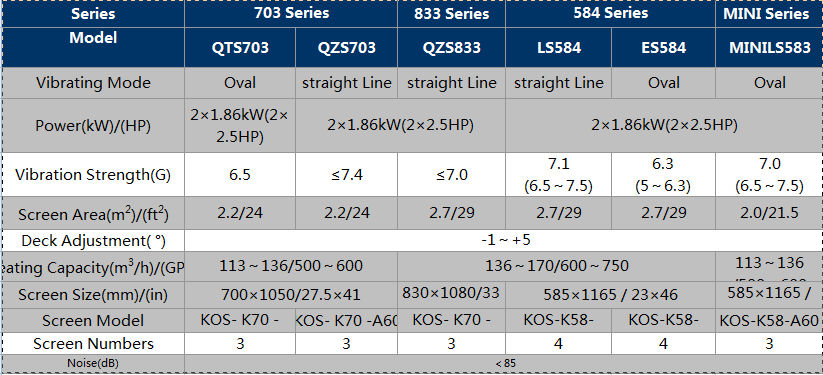
Drilling is widely used activity in oil and gas industry, to obtain deep seated fossil fuel to fulfill the fuel requirement across the globe, and that makes this industry quite enormous. The drilling operations are carried out on hard ground surface or on the ocean surface. In the entire drilling process, one of the main challenges is the handling of the drilling waste, it is called solid control system. The most important but easy to missed part is the shale shaker screen sizes application in real spot.
API being one of the largest trading group of US in drilling industry, has set up certain industry standards to test the quality of shaker screens, that are respected worldwide. Based on these tests, they have labeled different shaker screen sizes that approved by ISO, and encourage the shale shaker manufacturers like Kosun to use those labels on the product to enable the end user for a fair comparison before purchase.
While quality of different shaker screens cannot alone assure its performance, as the actual performance, in terms of conductance and life, will depend on a variety of aspects. To name a few – Handling of shaker screen, installation and replacement, appropriate tensioning, deck rubbers, storage and cleaning, volume of mud and solids, etc.